Taking Care Of Your Vinyl Records and the Science behind the Kirmuss record groove restoration process
PREAMBLE: Food for thought: Just as you need to care for your audio equipment, you also need to clean your records and care for them.
If they’re dirty it hardly matters how great your turntable is as your needle is not touching all the detail originally pressed in the record's groove by the stamper..
As such, Your music just won’t sound alive and exciting, no matter the price of your sound system.
You will not feel the breath of the artist or see the soundstage.
Cleaning the surface of the record while making it shiny which may make you feel good is not proper surface cleaning, or Kirmuss groove restoration.
Known cleaning processes just shine the record and inadvertently leave films that were air or vacuum dried onto the record. Sometimes even leaving residues from the original materials removed from the record, Why is this?
It is because both water with or without a soap added to a basin have the same electrical charge. As such, the record repels your efforts beyond surface cleaning. Water droplets as well are 100 to 110 micron diameter in size, they cannot "get into the smaller groove"..
You will also note where records processed manually or by vacuum or peer ultrasonic systems at the end of the process "pool water". A properly cleaned record repels water. Records should come out virtually dry.
Indeed all cleaning processes do something, removing surface dust, fingerprints, fungus, but music resides deep down into the record's grooves!
DISCOVER THE KIRMUSS PROCESS:
While ultrasonic cleaning processes uses mechanical vibrations to agitate a solution to aid in the removal contaminants, and where the sound waves created by the bottom mounted transducers that are excited by an ultrasonic generator in the bottom typically mounted on a stainless steel basin, sees these microbubbles rise. In so do doing as well as making contact with surfaces, the microscopic implosions of these rising bubbles create a vacuum-like scrubbing action dislodging contaminants from the record. This is the essence of cavitation. This does not accomplish the task at hand by itself. Proof: Keeping a record spinning in an ultrasonic basin will not see the effects of cavitation get down into the record's grooves alone.
>>> OUR IP: Only by ionizing the record and changing its charge to be opposite to that of water by using our spray brushed onto the record will the record now further attract this sonic plasma wave (pull) created by cavitation.
Thus: while other processes leave "a shine" on the record, we apply the spray and cycle the record in and out of the ultrasonic, this as the induced change of charge of the record wears off, Yet: each time removing a layer. Finally we now reach into the groove and remove the release agent that also sees dirt and dust particles fused into this "pressing oil" as they land on a hot, newly pressed record at the factory. These fused particles are the cause in most cases of the pops we hear when we play a new record.
HOW DO WE KNOW WHEN A RECORD HAS BEEN RESTORED?
The ionizing agent has a colorant added. As we cycle the record in and out of our machine, we see a whitish or grease-like materials appear when we reapply the spray with the supplied brush. As we cycle, we see first an increase in quantity, then a decrease, and just before the last cycle, the materials disturbed by the ultrasonic rapidly evaporate. Also, the record when wobbled sees water disperse. Placed horizontally on the workspace area, the record is virtually dry. Only a few drops of water to wipe off using a supplied optician's lint free cloth. To note where the droplets are 100-110 microns in diameter, much larger than the grooves themselves.
Your needle is now riding the detail as cut by the lathe that was hidden by this pressing oil.
AFTER KIRMUSS RECORD RESTORATION, no need to undergo this step process. As records do get handled and will see fingerprints once more on the surface, when deemed necessary, a 2 minute cycle suffices.
As records are stored in paper or HDPE or plastic record sleeves, records do breath and are "alive", where we see the plasticizer outgas when a record is stored in its sleeve. This leaves a film, so a 2 minute cycle as deemed appropriate by the owner can be performed.
Before playing any record, always use a 10 micron Parastatic felt brush to remove dust from the surface, Keeps your stylus clean. Then, followed by a 2.5 m Carbon Fiber Brush with a metal case to remove static. (Model KA-B1).
Store records vertically in a cool dry area away from sources of heat or direct sunlight. With records restored, slip them into HDPE anti-static record sleeves with an alkaline sandwiched filler (not rice paper)..
While one should discard paper sleeves as they may be ridden with fungus, do store them away from the record but easily retrieved if they have anything printed on them, adding value to your record for future resale.
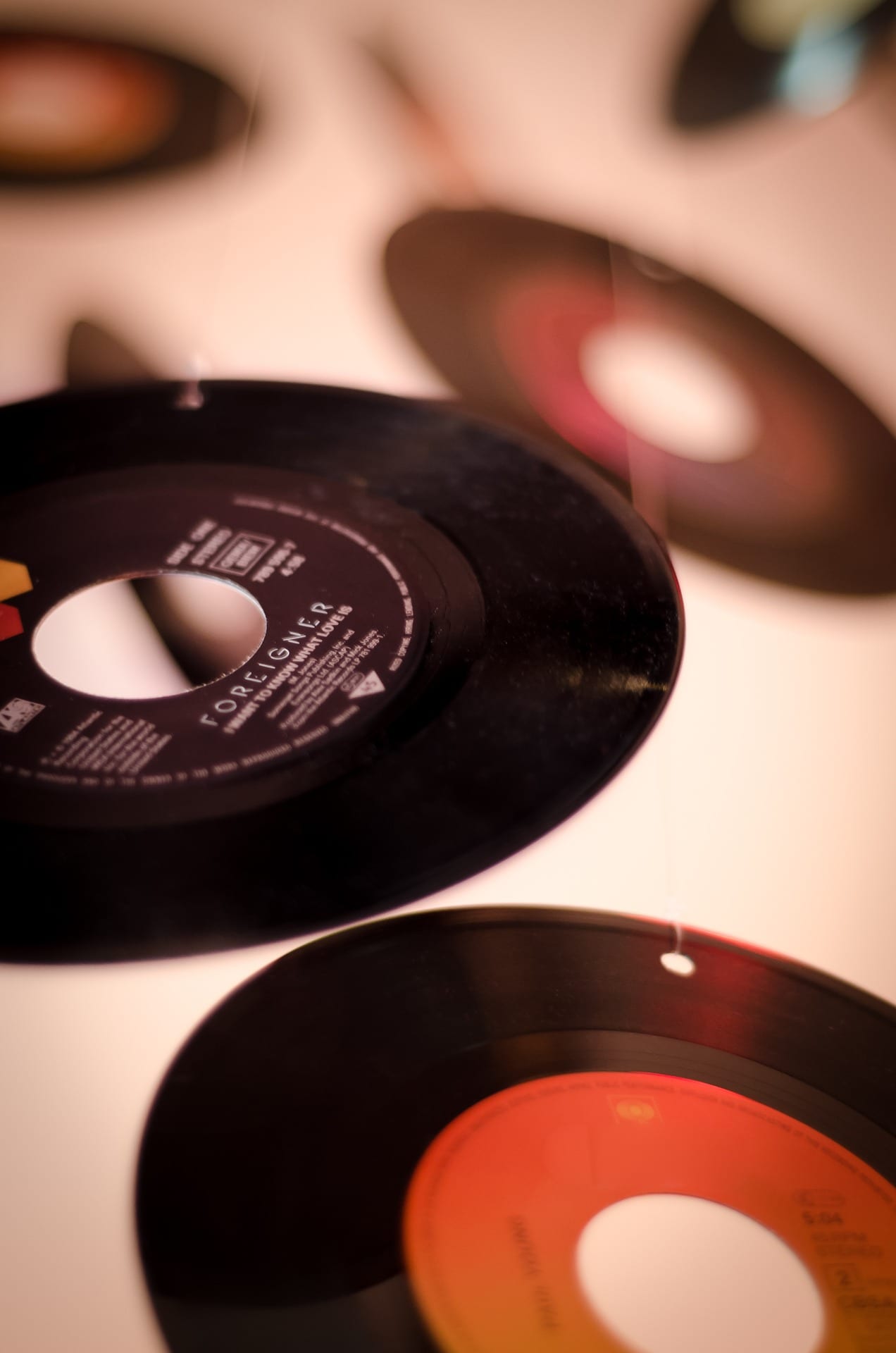
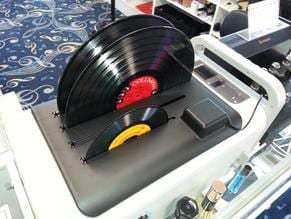
Keep your records clean!
The weakest link in your music experience is the source material. We know what compromises the CD and digital music have made for portability. Vinyl records are the oldest form of recordings and where you don’t want to let dirt, debris, fungus or other contaminants build up inside the grooves. Most forget where moist air with paper sleeves holding the records promotes the growth of fungus. Vacuum or air drying methods re-introduces dust and static as well as leaves residues in the grooves which sees the stylus no longer make proper contact with the pressing.
With our unique process and by removing the record's release agent, sometimes present for 30, 40 and 50 years and even in the latest pressings, all records are often redeemable. WITH THE NEEDLE NOW MAKING PROPER CONTACT WITH THE GROOVE, even light surface scratches while originally thought permanent in most cases are no longer touched by the needle's dyne and are now transparent. Seven times out of 10 we may also recover and not hear the click associated with a tone arm skid, just because the needle is now riding in effect what the stamper had as detail, less release agent.
Improper storage and handling can also affect your records. Keep in a dry, well ventilated area. Replace paper sleeves with anti-static, anti-fungal, 4 mil HDPE sleeves. (also available from us (Model KA-RS-1-40). DO NOT THROW OUT PRINTED PAPER SLEEVES. While they may be ridden with fungus, store them separate to the record as mentioned where they may add value to your record.
Handle record by the edges.
"One thing is certain: playing a dirty recording, regardless of its format, is one of the most damaging things you can do to it.”
-(Gerald L. Gibson, Head of the Motion Picture, Broadcasting, and Recorded Sound Division of the Library of Congress, 1991)
The good news? Caring for your records isn’t all that hard.
By using the Kirmuss Audio Record Restoration System you’ll never have to worry about dirty records getting between you and your music as the release agent left over from the pressing process has been removed.
To remember: Most processes cosmetically clean the record’s surface, and most leave a coating or residue in the grooves. Vacuum systems also introduce dust and apply static, also leaving residues on the groove surface. The KirmussAudio process strips out lodged contaminants from the grooves, including removal of the original record release agent that may in fact see dust, dirt, and fungus lodged in the grooves.
Grooves are the key to great sound
Record grooves are where your favorite music lives. As your stylus cruises the grooves, it sends those analog signals through the cartridge to your preamp and, finally, to your speakers.
Grooves are essentially to records and with release agent removed with the needle riding "in the pocket", what words are to a novel and just as you can’t tell a great story without compelling language, you can’t enjoy great sound without both surface cleaning and groove restoration, removing the release agent.
Why store records vertically?
Stacking records can warp or bend them. Record shops don’t display vinyl vertically just for customer convenience.
They do it to protect their product.
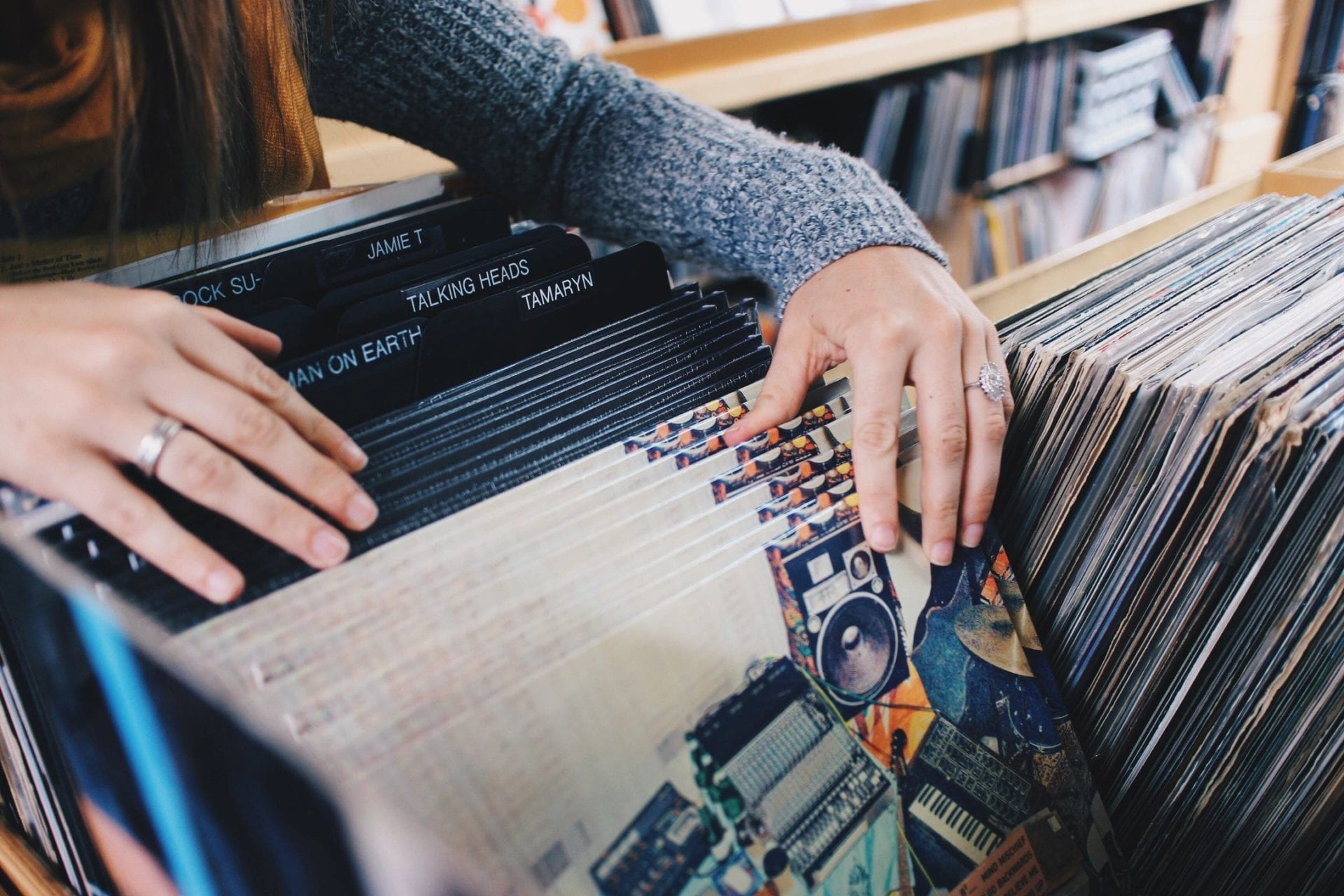