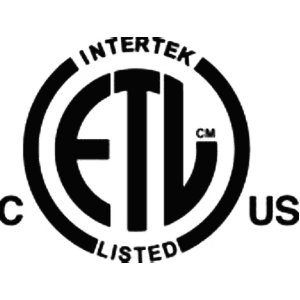
The KA-RC1 is ETL Approved!
ETL is a mark provided by Intertek, a Nationally Recognized Testing Laboratory that is found on our washer where ETL tests products to UL, CSA and CE standards.
A product bearing the ETL Listed Mark is determined to have met the requirements of prescribed product safety standards as well as where our factory conforms to a range of compliance measures and is subject to periodic follow-up inspections to verify continued conformance.
Beware: Not All Ultrasonic Machines Wash Your Records Safely!
You Must Specify 35 Khz!
"Sonically speaking" indeed where higher the frequency, the smaller the bubbles, smaller the bubbles, they enter small crevices easier.
A RECORD, CONTRARY TO POPULAR BELIEF IS NOT A SMALL CREVICE!
MINUTE DETAILS WITHIN THE GROOVE PROVIDE TIMBER AND THE EXCELLENCE OF ANALOG.
THESE INDENTATIONS SHOULD NEVER BE REMOVED!
In 3 years of testing, we have concluded that 35 kHz is the "sweet spot"; that frequency does not remove these details and does not "smoothen" the grooves as would a poorly designed record cleaner leaving a residue which has the same effect. Not 45, not 80, not 90 kHz. NEVER 120 kHz or higher. All are proven to damage records over time. Much misinformation out there: We have in house experienced engineers familiar with ultrasonic generation. 35 kHz is gentle yet powerful to do the job!
A Primer on Sonic Technology:
Under pressure of continuous vibration by the ultrasonic generator at the bottom of the tank bubbles generated rise and stretch and compress at a fast rate. Once they reach a certain size as determined by the frequency and strength of the sound waves produced the bubbles lose structural integrity and collapse violently. When these implosions happen near the surface of an object such as a record, the bubbles emit high-powered streams of plasma that travel at more than 500 miles per hour and collide with, agitate and remove even very tiny particles and substances from the record's surface. Using a surfactant attracts further these bubbles to the record. (For new records, 40 mL of 70% alcohol per 6 L of distilled water to remove record pressing residue, our 1% propanol as a second step is a surfactant brushed in to aid in the removal of fungus as well as remnants of past manual, vacuum and ultrasonic systems and air or forced blow drying techniques, stripping these residues. THAT IS WHY WE RESTORE A RECORD AND NOT JUST COSMETICALLY CLEAN AS DO OTHERS!
To this and CALLED CAVITATION: In an ultrasonic cleaning machine, explosions occur millions of times per second, with resulting explosions and wave being attracted by our surfactant brushed in thus removing contaminants.
Technically: Bubble size relates to how much energy is released when they implode. That’s why while a higher frequency yields more bubbles it’s a better choice for cleaning parts with very tiny features such as blind holes, channels and threads. This a danger for vinyl and shellacked records.
When they explode, the small bubbles CAUSE a PLASMA WAVE that could damage the depth of the groove; thus removing timber and high frequencies. AFTER 4 YEARS OF TESTING we have found that THE BEST ULTRASONIC FREQUENCY is 35 kHz with a maximum temperature of 95°F. Higher frequencies such as 100, 125, 130 kHz are used for fine cleaning jobs as they enter small surfaces including microelectronics, printed circuit boards, medical and precision optics where the resulting higher intensity powerful plasma explosions remove post manufacturing matter and dirt suited to those materials. Records need specific cleaning attributes.
The 35 kHz frequency with our ceramic generator and element combined with our record spacing of a maximum of 4 records per a 6 litre tank offers a good combination of power, penetration, and very even energy distribution that can successfully address record cleaning applications.
Our properly-engineered cleaning system does not damage the stainless steel basin as do higher frequencies.
A 2 minute cycle allows us to restore a shellacked record (78's).
AVOID HOME MADE SYSTEMS WHERE TEMPERATURES EXCEED 95°F, (35°C) as these WARP RECORDS and affect groove integrity.